
Nike’s montebelluna factoryimage © designboomĭetailed perspective of a machine in the manufacturing line for the nike GS bootimage © designboom The station where rubber cement is applied to the bootimage © designboomĪn additional view of the italian nike production facilityimage © designboomīoot-shapers and half completed shoes wait on a shelving systemimage © designboom solvent free-laces – 70% recycled polyester-foam – soy based, made of 15% palm oil, a renewable resource-toe board –17% recycled material and all waste is re-used to create a closed loop product-tongue- made of 95% recycled materialĪ view of the nike GS signage within the small factoryimage © designboom ‘green’ aspects of the nike GS green speed:-quarter/tongue – 95% recycled material-reinforcement – 20% renewable material-collar – 15% renewable + 32% recycled polyester-lining – 88% recycled polyester / 12% pu. Graphic breakdown of the boot’s componentsimage © designboom The boot ready for packagingimage © designboom The underside of nike’s newest bootimage © designboom Resting for a moment as the form fits the shape of the mouldimage © designboomĮach shoe is outfitted with the flag of the country that wears the bootimage © designboom
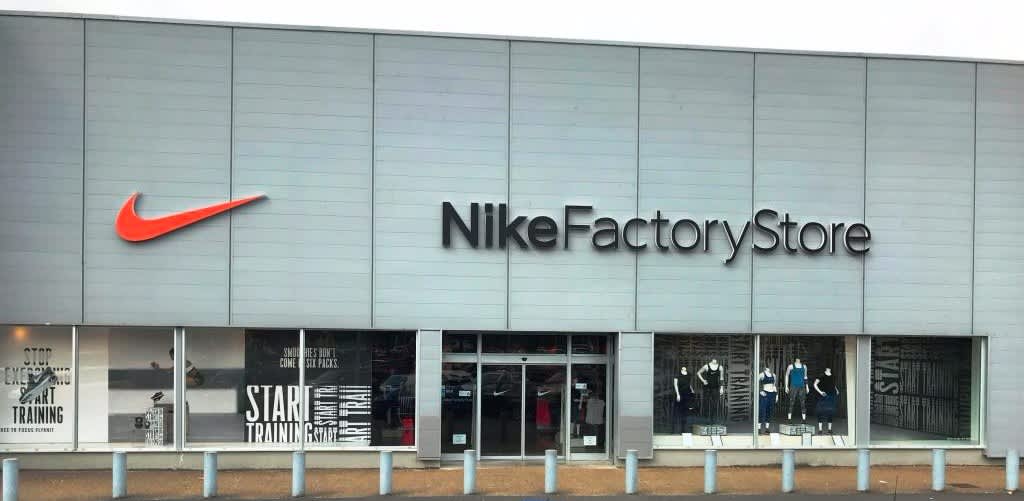
Pulling the toe and upper into formimage © designboom Moulding the upper over the toe boardimage © designboom
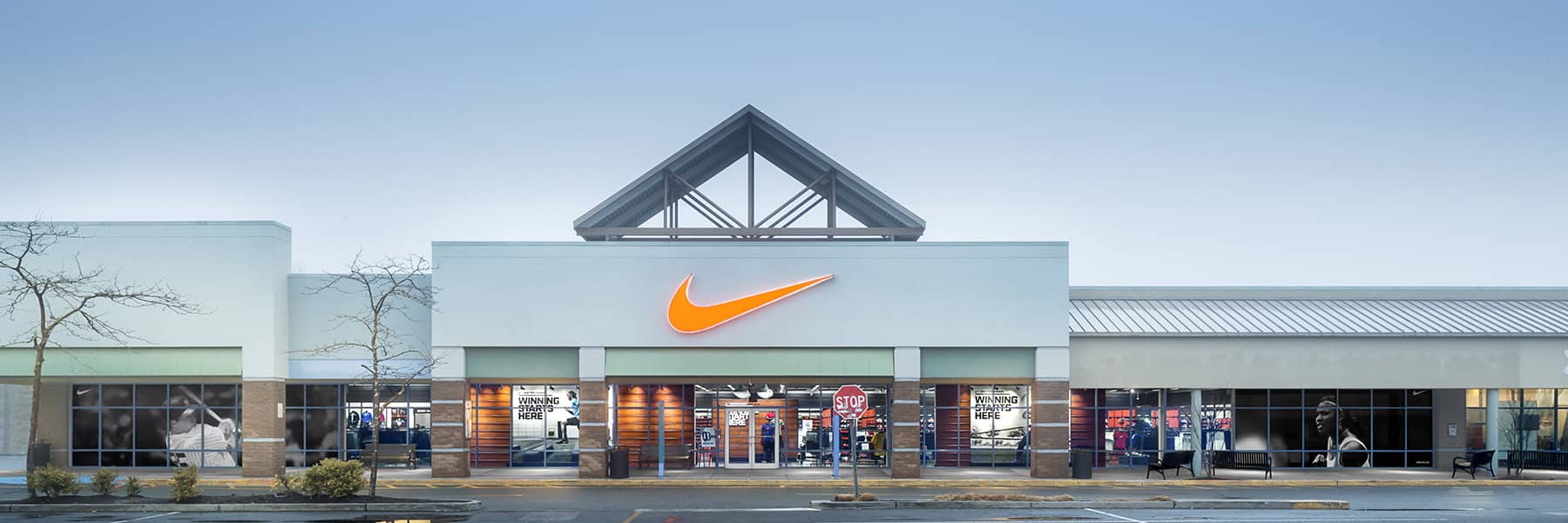
Individual components of the shoeimage © designboomĭesignboom’s nike greenspeed factory visitvideo © designboom Segments of the shoe in varied states of constructionimage © designboom the concept boot is not formed from 100% recycled matter and energy, yet it is the first wide-reaching production demonstration by nike of the potential for sustainable or low-impact design in the development of high-performance football boots. the laces, tongue and lining of the nike gs, are formed from a minimum of 70% recycled materials while the collar and toeboard have a material makeup including least 15% recycled matter. The traction plate of the boot is crafted from a mix of material including 50% castor beans and 50% plastic where the sock liner is made from 100% castor beans. our behind-the-scenes look at nike’s production facility pictures the efforts made by nike’s team of creatives to develop the lightest and most minimal shoe available form their brand, observing the construction of their sustainable soccer shoe from start to finish. within this cozy italian factory, an innovation team, product development team and production group, comprised of 15 individuals with a collective experience of 350 years in footwear, were able to build the nike GS. the region is known for its rich history of artisan shoe construction in italy– a country world renowned for their skill in the production of artisan footwear. Nike’s selection of this particular location for their manufacturing plant is no coincidence. though the corporations’ roots are in the united states, their factories and niketown stores are found all over the globe. is the world’s largest, most recognizable and most profitable organizations in the filed of sports business. Nike was founded in 1964 in beaverton, oregon, USA, under the name ‘blue ribbon sports’ by bill bowerman and phil knight as a sportsware and equipment manufacturing company. The materials which comprise each shoe made in the small factoryimage © designboom we’re happy to offer our readers images and a video of the making process.
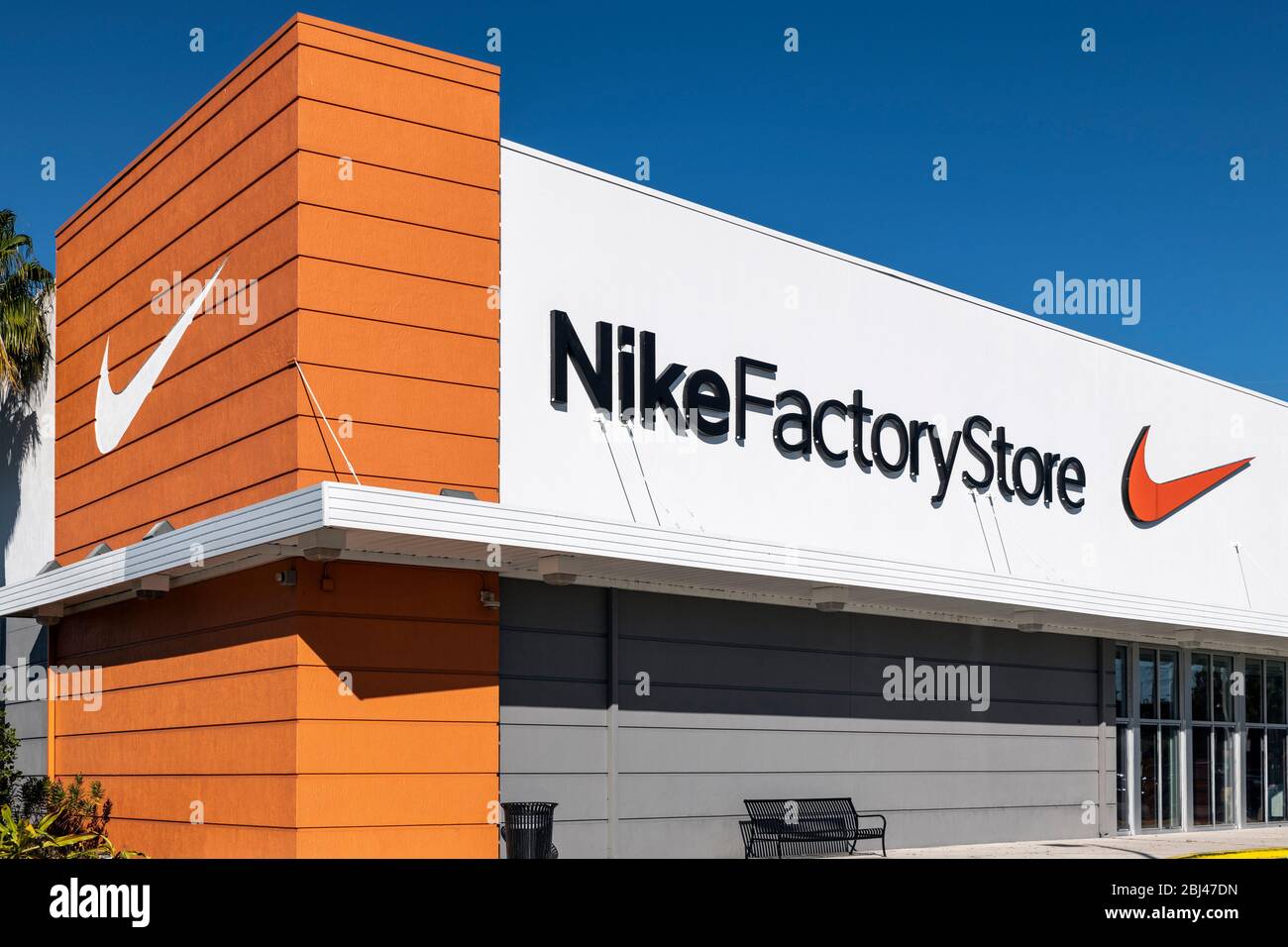
#Nike factory professional#
the facility specializes solely in the production of the brand’s top-of-the-line, professional athletic boots and is located in montebelluna just forty minutes from the city of venice in the countryside for nike’s newest and lightest football boot, the NIKE GS (or green speed).
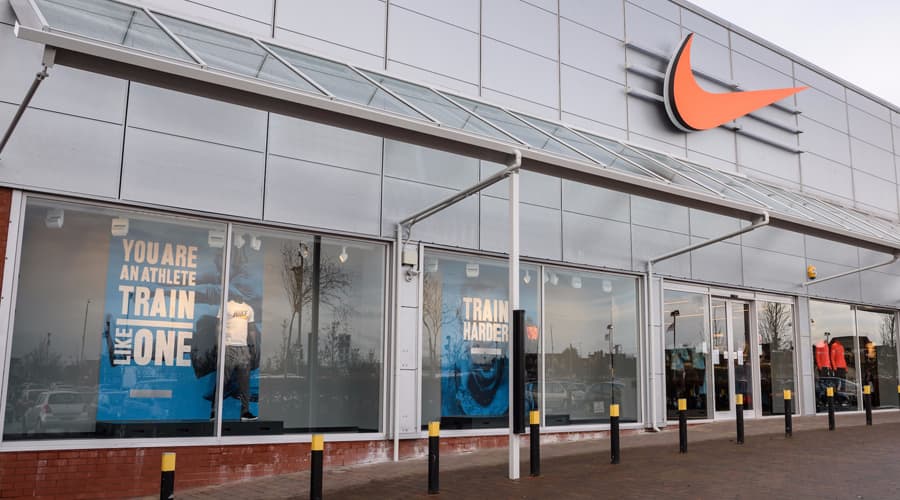
A few days ago, designboom visited NIKE‘S small and exclusive italian factory.
